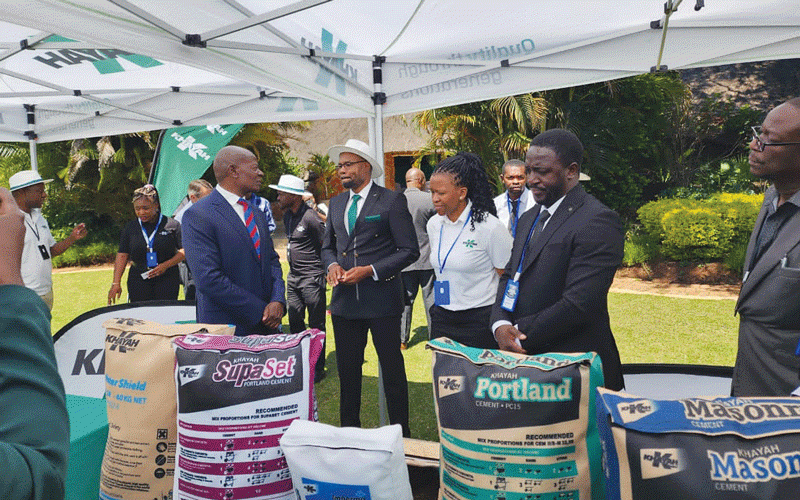
CEMENT manufacturer Lafarge Cement Zimbabwe has concluded the implementation of its US$25 million capital expansion programme earmarked to improve cement milling capacity and automate the dry mortar mix (DMX) plant.
In addition to the expected increase in production capacity, the programme is also expected to create infrastructure to improve power supply and cement storage.
“The business concluded the implementation of the previously announced US$25 million capital expansion programme,” Lafarge chairperson Kumbirai Katsande said in a statement accompanying the group’s financial results for the year ended December 31, 2022.
“The final phase of this three-pronged investment plan was the commissioning of the vertical cement mill (VCM) in 2022, following the successful installation of alternative power infrastructure in 2020 and the completion of the automated dry mortars plant in 2021.”
Katsande said the company, which was taken over by Fossil Mines last year, would also continue to adapt its business strategy so as to thrive in the ever-changing environment.
“Encouraging signs are being observed in the individual household sector and government-funded infrastructure projects. There is also higher economic activity in the agricultural sector which is being spurred by government-driven initiatives.
He added: “The company is uniquely positioned to support the agricultural sector through its dry mortar products which include agricultural lime. Consequently, the directors are satisfied with the positive trend in production, sales and profitability recovery despite power outages, and that overall performance will continue improving going forward.
“The change of the company’s name from Lafarge Cement Zimbabwe Limited to Khayah Cement Limited will be dealt with at the forthcoming EGM [extraordinary general meeting] scheduled for July 7, 2023. This will pave the way for resumption of trading of the company’s shares on the Zimbabwe Stock Exchange.”
- Inaugural Zim investor indaba highlights
- Stop clinging to decaying state firms
- ZB explores options to tackle inflation
- Zim operations drive FMB Capital
Keep Reading
The chairperson bemoaned the influx of cheap imported cement, saying it posed a serious threat to the domestic industry which has enough capacity to meet national demand.
“Constructive engagement continued with the regulatory authorities in an endeavour to obtain the required support,” he said.
The company resumed production of cement at both mills in mid-February 2022 following the October 2021 incident which resulted in the roof over both cement mills collapsing.
During the second half of the year, Katsande said the company successfully commissioned the VCM and subsequently decommissioned Mill 1 which had the least capacity.
The VCM doubled the company’s milling capacity to one million tonnes per annum and bolstered its ability to supply high strength cement of improved quality and, at the same time, reduced production costs.
In December 2022, there was a change of the company’s majority shareholding which saw a local consortium acquire 76,4% stake in the business, previously held by Associated International Cement Limited.
Accordingly, the company embarked on a transformation and rebranding journey in line with the changes in the majority shareholding.
Inflation-adjusted revenues were constant at $24,4 billion over the comparative period.
Cement production volumes decreased by 15% following the cement mill roof collapse incident.
Production ramp up after the commissioning of the VCM was also slow as tests had to be conducted before the mill could perform at optimal level.
Sales volumes decreased by 19% in line with the trend in production volumes.
The company also witnessed increased costs as a result of increased third party and plant maintenance costs.
Consequently, margins dropped to 32,5% compared to 49,6% in the prior year.
The company managed to maintain tight control over its operating expenditure as total expenses fell by 7,6%.
Distribution expenses declined by 77,1%, while administrative costs remained fairly constant over the comparative period.
Despite the operating cost containment efforts, the lower volumes and inflationary pressures weighed down the overall performance of the company to a loss before tax of $17,3 billion compared to a profit before tax of $1,7 billion in 2021.
Exchange rate losses increased by 490% and were the major driver of the decline in profitability.
The dry mortar business performance was adversely affected by raw material shortages, including key imported materials, owing to foreign currency shortages.
The company had net long-term borrowings of $9,2 billion for the year under review.